Mit 3D-Druck zum Prototypen: Verfahren und Vorteile des Rapid Prototyping
- 27. Apr. 2023
- 9 Min. Lesezeit
Aktualisiert: 14. Feb. 2024
Zeit einsparen, Gewicht reduzieren, Materialverbrauch minimieren: Immer mehr Branchen und Unternehmen setzen auf die verschiedenen Verfahren des Rapid Prototyping (Abk. RP), um Prototypen herzustellen. Ursprünglich kam Rapid Prototyping bei der Fertigung von Teilen und maßstabsgerechten Modellen für die Automobilindustrie zum Einsatz. Mittlerweile umfasst der Begriff neben der Herstellung von Prototypen auch das Rapid Tooling – also das schnelle Herstellen von Werkzeugen – und das Rapid Manufacturing – das schnelle Herstellen von Kleinserien, Einzelstücken und Ersatzteilen.
Die Liste der Verfahren beim Rapid Prototyping ist lang: Zu den bedeutendsten gehören verschiedene 3D-Druckverfahren, die das Modell Schicht für Schicht aufbauen. Die sogenannte additive Fertigung des 3D-Druckers unterscheidet sich grundlegend von subtraktiven Fertigungsverfahren wie dem Bohren, Fräsen oder Schleifen. Bei diesen traditionellen Methoden wird Material entfernt, um Teile herzustellen.
Als Schlüsseltechnologie der Industrie 4.0 ist der 3D-Druck in fast allen Branchen auf dem Vormarsch: von der Luft- und Raumfahrt über Architektur und Medizintechnik bis zu Design und Kunst. Auch in der Konsumgüterbranche mit kundenindividuellen Anforderungen an die Fertigung ist Rapid Prototyping nicht mehr wegzudenken.
Ein aktuelles, eindrucksvolles Beispiel für die Möglichkeiten der additiven Fertigung bildet eine Trägerrakete des US-amerikanischen Herstellers Relativity Space. 85 Prozent der Raketenmasse wurden mit dem 3D-Drucker – im selektiven Laserschmelzverfahren – aus Metalllegierungen hergestellt. Nach Angaben der Betreiberfirma ist die "Terran 1" das größte jemals mit einem 3D-Drucker produzierte Objekt.
Doch welche Vorteile bringt die additive Fertigung? Welche Druckverfahren kommen in der Industrie zum Einsatz und worin unterscheiden sich diese untereinander?
Die wichtigsten 3D-Druckverfahren: Filament, Pulver oder Flüssigkeit
Zunächst lässt sich festhalten, dass alle 3D-Druckverfahren schichtweise arbeiten: Bei der Modellierung wird Material aufgetragen beziehungsweise hinzugefügt, und zwar so lange, bis das gewünschte Objekt entstanden ist.
Als Basis für den Fertigungsprozess dient ein 3D-Konstruktionsmodell, das mithilfe einer Schneidesoftware, auch Slicer genannt, in Schnittkonturen zerlegt wird: Jede Schicht bildet einen Querschnitt durch das Bauteil und repräsentiert eine Schicht während des Druckprozesses. In solch einem Programm wird das digitale Modell in eine Steuerdatei für den 3D-Drucker umgewandelt. Das Ergebnis ist zum Beispiel in G-Code, der gängigsten CNC-Programmiersprache, die auch bei 3D-Druckern Verwendung findet.
Grundsätzlich lassen sich additive Verfahren in drei Kategorien einordnen, und zwar auf Basis des verwendeten Werkstoffes: Filamente (auf Spulen), pulverförmiges und flüssiges Material. Die jeweiligen Verfahren unterscheiden sich dabei maßgeblich: Je nach Technologie legt der 3D-Drucker durch eine Düse oder Öffnung Material ab, verschmilzt Pulver mittels Laser oder härtet Photopolymere mit UV-Licht.
Wir geben Ihnen eine Übersicht aktueller 3D-Druckverfahren in der Industrie.
3D-Druckverfahren mit Filamenten: FDM
Beim FDM-Druck (Fuse Deposition Modelling; auch FFF: Abk. für Fused Filament Fabrication) wird drahtförmiges Material – sogenanntes Filament – von einer Spule abgewickelt, durch Erhitzung verflüssigt und mit einer Düse, dem Extruder, Schicht für Schicht zu einer dreidimensionalen Form auf dem Druckbett aufgebaut. Genauer gesagt, entsteht ein sehr feiner Kunststoff-Faden, der nach und nach die einzelnen Modellschichten formt und anschließend aushärtet (siehe Abbildung). Der Druckkopf ist meist so programmiert, dass er sich über die horizontale Achse (X-Y) bewegt, während – je nach Druckermodell und Hersteller – das Druckbett der Maschine für die vertikale Achse (Z) zuständig ist. Bei komplexen Objekten mit Überhängen sind Stützstrukturen notwendig.

Anmerkung zur Abb.: Abhängig vom jeweiligen FDM-Drucker kann das Druckbett fest oder beweglich sein.
3D-Druckverfahren mit Pulver: SLM, SLS, EBM und BJ
„Powder Bed Fusion“: Bei diesen 3D-Druckverfahren wird anstelle von Filament Materialpulver verwendet, das selektiv entlang der vorher festgelegten Strukturen durch Hitze oder bestimmte chemische Prozesse gebunden wird. Dazu zählen das weit verbreitete SLM – selektives Laserschmelzen – als auch das SLS – selektives Lasersintern – sowie das selektive Elektronenstrahlschmelzen (EBM) und das Binder Jetting (BJ). Die Unterschiede in den Pulverbettverfahren bestehen hauptsächlich in der Art und Weise, wie das Pulver gebunden wird.
Bei ersterem Verfahren, dem Selektiven Laserschmelzen (Abk. SLM für Selective Laser Melting), wird der zu verarbeitende Werkstoff in Pulverform – meist Metall – in einer Druckkammer hauchdünn und gleichmäßig mit einem Schieber oder einer Walze auf einer Grundplatte verteilt. Ein Laserstrahl schmilzt das Pulver vollständig bei Temperaturen über 1.000 °C – überall dort, wo laut CAD-Datei das Bauteil entstehen soll. Anschließend muss die geschmolzene Schicht aushärten, woraufhin die Grundplatte abgesenkt und eine neue Schicht Pulver aufgetragen wird. Dieser Prozess wiederholt sich, bis alle Schichten umgeschmolzen sind und das Werkstück vollständig ist. Das fertige Bauteil wird abschließend vom überschüssigen Pulver gereinigt. Das Material, das während der Fertigung nicht verbunden wurde, kann beim nächsten 3D-Druck erneut verwendet werden.
Ähnlich wie das SLM funktioniert das Selektive Lasersintern (Abk. SLS für Selective Laser Sintering). Auch hier wird mittels Laser Material – vor allem Kunststoff – schichtweise geschmolzen (siehe Abbildung). Der wesentliche Unterschied beider Technologien liegt im zugrundeliegenden Schmelzverfahren: Beim Sintern ist die Temperatur nicht hoch genug, um das Material vollständig aufzuschmelzen. Es wird nur so weit erwärmt, dass sich die benachbarten Materialpartikel verbinden (partielle Partikelverbindung).
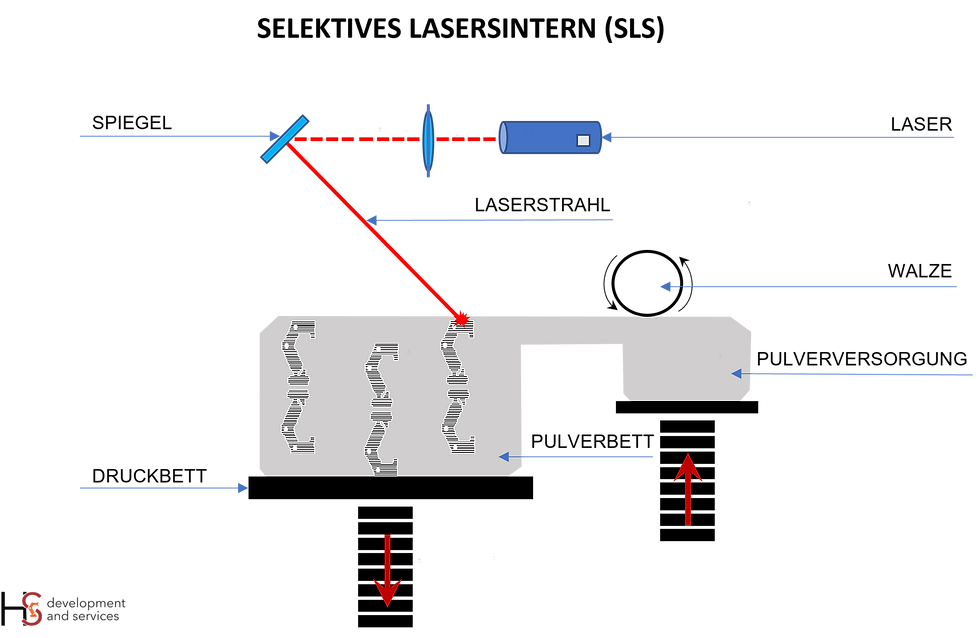
Ein ebenfalls pulverbasierter Prozess im Bereich der additiven Fertigung ist das Elektronenstrahlschmelzen (Abk. EBM für Electro Beam Melting). Der Unterschied wird schon an der Bezeichnung deutlich: Anstelle eines Lasers wird hier ein Elektronenstrahl als Wärmequelle verwendet, um Metallpartikel zu verschmelzen und Schicht für Schicht das gewünschte Bauteil zu erzeugen. Da das Elektronenstrahlschmelzen auf dem Prinzip der elektrischen Ladung basiert, müssen die verwendeten Materialien leitfähig sein.
Beim Binder Jetting (Abk. BJ) wird pulverförmiges Material an ausgewählten Stellen mit einem Bindemittel verklebt. Genauer: Das flüssige Bindemittel wird mit tintenstrahldruckerähnlichen Druckköpfen auf die programmierte Kontur aufgetragen. Nachdem eine Pulverschicht angemessen gebunden ist, senkt sich die Bauplattform ab. Nun beginnt der Drucker erneut, selektiv weitere Tröpfchen des Bindemittels aufzubringen, um die zweite Schicht zu bilden – bis das Werkstück vollständig ist. Das Besondere beim Binder Jetting: Material und Bindemittel können während des Druckes gewechselt werden.
3D-Druckverfahren mit flüssigen Materialien: SLA und DLP
In diese Kategorie fallen unter anderem die Stereolithografie (Abk. SLA für Stereo Lithography Apparatus) und das Digital Light Processing (Abk. DLP). Anders als bei den Pulverbettverfahren ist das Ausgangsmaterial hier flüssig: Basis der 3D-Druckverfahren ist ein Becken voller lichtempfindlichen Kunstharzes, sogenanntem Photopolymer, das beim Kontakt mit Licht aushärtet. Während SLA-3D-Drucker UV-Laser verwenden, um das Kunstharz auszuhärten, nutzen DLP-Drucker UV-Lichtprojektoren.
Während der Belichtungszeit trägt der SLA-Drucker das Kunstharz exakt in der vorgegebenen Form auf die Druckplatte auf. Über die flüssige Schicht fährt ein Laser, der von einem Computer über bewegliche Spiegel gesteuert wird. Ist diese Schicht erstarrt, so wird die Druckplatte nach unten gezogen und es entsteht die nächste Schicht auf dieselbe Art und Weise. Dieser Vorgang wird so lange wiederholt, bis das 3D-Modell vollständig aufgebaut ist. Alternativ wird das Bauteil am Grund des Behälters gedruckt, wobei die nächste Schicht nach oben aufgetragen wird (siehe Abbildung). Da sich das gesamte Werkstück während des Fertigungsprozesses in einem Flüssigkeitsbad befindet, sind Stützstrukturen notwendig. Abschließend wird das Modell in UV-Licht nochmals ausgehärtet und die Stützstrukturen werden von Hand entfernt. Gut zu wissen: Das Stereolithografie-Druckverfahren wurde bereits in den 80er Jahren entwickelt und ist damit das älteste 3D-Druckverfahren der Welt.

Beim Digital Light Processing wird ein Projektor als Lichtquelle verwendet, um die Photopolymer-Harze auszuhärten. Grundsätzlich ähnelt dieses Vorgehen dem SLA-Verfahren. Das DLP-Druckverfahren setzt eine digitale Leinwand ein – einen Chip mit zahlreichen Mikrospiegeln (Abk. DMD für Digital Micromirror Device) – um das Bild einer Schicht auf die gesamte Plattform zu projizieren, wodurch alle Punkte gleichzeitig gehärtet werden.
Industrielle Anwendung: Rapid Prototyping, Rapid Manufacturing und Rapid Tooling
Und was lassen die Unternehmen mit dem 3D-Druck herstellen? Grundsätzlich ist zwischen der Herstellung von Modellen, Prototypen und Einzelstücken (Rapid Prototyping) einerseits und der Fertigung von Kleinserien und Ersatzteilen (Rapid Manufacturing) sowie von Werkzeugen (Rapid Tooling) andererseits zu unterscheiden.
Das schnelle Herstellen von Prototypen während der Entwicklungsphase verkürzt die Dauer bis zur Produktreife. Unternehmen können zeitnah verschiedene Versionen eines Prototyps entwerfen, anstatt die Leistung auszulagern. Die Anwendung von 3D-Druckverfahren endet jedoch nicht bei der Herstellung von Modellen und Prototypen, sondern hat sich mittlerweile auf die Fertigung von Kleinserien ausgeweitet. Gerade bei Kleinteilen kann Rapid Prototyping noch bei Stückzahlen von mehreren 10.000 Stück interessant sein. Mit der fortschreitenden Entwicklung der 3D-Drucker – schnellere Druckgeschwindigkeit, Arbeit mit mehreren Lasern oder Druckköpfen gleichzeitig – werden die Stückzahlen sehr wahrscheinlich weiter steigen.

Die Wahl des passenden 3D-Druckverfahrens hängt wiederum von mehreren Faktoren ab: Material, Form und Stückzahl spielen dabei eine wichtige Rolle. Je nach Beschaffenheit des Materials ergeben sich unterschiedliche Vor- und Nachteile, die oft maßgeblich für die Entscheidung für ein Verfahren sind. Die grundlegende Frage lautet: Für welches Anwendungsgebiet brauche ich das jeweilige Bauteil und welche Anforderungen habe ich an das fertig gedruckte Objekt?
Generell lässt sich festhalten, dass Filamente auf Spulen – wie sie beim FDM-Druck zum Einsatz kommen – schnell und einfach verarbeitet werden können. Damit sind sie für den Prototypenbau oder für Teile mit größeren Toleranzen besonders geeignet. Pulverförmige Materialien – bei Powder Bed Fusion – hingegen sind für präzise Bauteile zu bevorzugen, die gleichzeitig hohen Belastungen standhalten müssen. Mithilfe des Lasers lässt sich das feine Pulver exakt und dicht verschmelzen. Um hochkomplexe und exakte Bauteile herzustellen, welche nicht stark belastet werden müssen, eignen sich wiederum flüssige Materialien wie Harze, die bei SLA- und DLP-Druckern das Ausgangsmaterial bilden.
Bisher konnten sich in der Industrie vor allem Techniken zur additiven Herstellung von Kunststoff- und Metallbauteilen etablieren. Die Entwicklung geht aber auch dahin, dass andere Materialien wie Sand, Glas, Beton oder Keramik im 3D-Druck zum Einsatz kommen – bis hin zu Lebensmitteln oder menschlichen Zellen.
Additive versus subtraktive Fertigung
So viel zu den unterschiedlichen Anwendungsgebieten und zum Vergleich der Eigenschaften der additiven Fertigungsverfahren untereinander. Aber sind 3D-Druckverfahren in allen Bereichen der klassischen subtraktiven Fertigung überlegen?
Zur Erinnerung: Subtraktive Verfahren zeichnen sich dadurch aus, dass Material weggenommen bzw. abgetragen wird. Ausgangsstoffe sind feste Blöcke oder Stäbe aus Metall, Kunststoff oder anderen Materialien, die geformt werden, indem Material durch Schneiden, Bohren, Spanen, Fräsen oder Schleifen entfernt wird. Diese Verfahren werden entweder von Hand durchgeführt, oder – in den meisten Fällen – durch eine numerische Steuerung (Computer Numerical Control, CNC), welche die Werkzeugmaschinen steuert. Die Fertigungsanlage benötigt ein virtuelles, mithilfe von CAD-Software erstelltes Modell als Input. Die subtraktive Fertigung gilt als traditionelle Methode in der industriellen Herstellung.
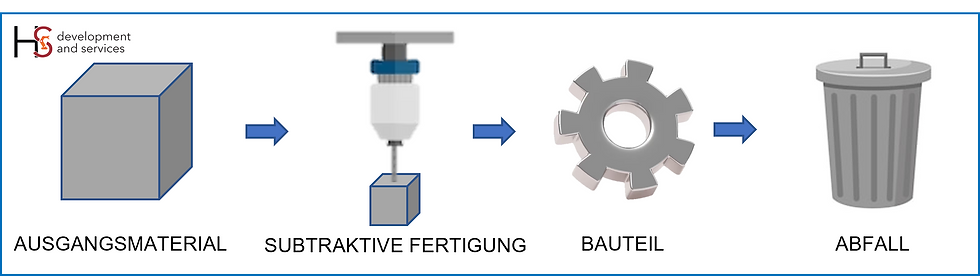
Die Stärke von subtraktiven Methoden liegt in der hohen Maßgenauigkeit bzw. Präzision sowie in der großen Auswahl an kompatiblen Materialien. So ist es beispielsweise möglich, Teile aus Metall – unabhängig vom Schmelzpunkt –, Kunststoff oder Holz auf ein und derselben Maschine herzustellen. Dabei lassen sich unterschiedliche Oberflächenbeschaffenheiten von glatt bis rau realisieren als auch verschiedene Materialeigenschaften wie Härte oder Duktilität durch nachträgliche Oberflächenbehandlungen. Die hohen Werkzeugkosten amortisieren sich über hohe Stückzahlen identischer Teile: Die Kosten sinken stetig, je mehr Teile hergestellt werden. Nachteilig sind die lange Vorbereitungszeit bis zum Produktionsstart, die vergleichsweise große Menge an Abfall, der bei der Herstellung anfällt und der Aufwand bei der Herstellung. Ein Objekt erfordert manchmal mehrere Arbeitsschritte, die Verwendung verschiedener Maschinen und die Aufteilung in mehrere Teile, die wieder zusammengesetzt werden müssen. Das Design wird durch die verwendeten Werkzeugmaschinen eingeschränkt. Designänderungen lassen sich meist nur langsam umsetzen.
Die Vorteile des Rapid Prototyping liegen auf der Hand: Mithilfe von 3D-Druckern lassen sich individuelle Modelle, Prototypen oder Werkzeuge schnell und kosteneffizient direkt vor Ort fertigen. Nach der Erstellung des 3D-Modells kann direkt mit der Produktion begonnen werden. Zwischen Dateneingang und Auslieferung der Teile vergehen meist nur ein bis fünf Arbeitstage. Dabei herrscht eine große Form- bzw. Designfreiheit: Mit additiven Verfahren lassen sich geometrisch komplexe sowie filigrane Objekte drucken und das ganz ohne zusätzliches Werkzeug. Reale Anschauungs- oder Funktionsmodelle helfen dabei, Fehler in der Konstruktion oder Konzeption schneller zu erkennen und können Innovationsprozesse beschleunigen. Änderungen im Design lassen sich schnell umsetzen. Ein weiterer Vorteil ist eine flexible, dezentrale Produktion bei Bedarf (on demand). Lagerhaltung und die Logistikkosten können so reduziert werden. Außerdem können Lieferengpässe für kritische Bauteile überbrückt werden – gerade in Krisenzeiten. Für die kundenindividuelle Fertigung eröffnet der 3D-Druck vielfältige Möglichkeiten.
Im Vergleich zu den klassischen subtraktiven Verfahren werden bei additiven Fertigungsverfahren die Teile nach exakten Vorgaben der CAD-Datei mit dem digitalen Bauplan des Produkts hergestellt, wodurch der Materialverlust äußerst gering ausfällt. Zudem kann Pulver bei pulverbasierten Prozessen, das nicht aufgeschmolzen wurde, in den meisten Fällen für das nächste Projekt wiederverwendet werden. Gleichzeitig ermöglichen additive Fertigungsverfahren neue Produkteigenschaften oder differenzierten Materialeinsatz. Knappe Ressourcen wie etwa seltene Erden können auf diese Weise eingespart oder subsituiert werden. All diese Punkte machen Rapid Prototyping zu einem kosteneffizienteren und ökologisch nachhaltigeren Verfahren im Vergleich zu traditionellen Fertigungsmethoden.
Allerdings sind die relativ hohen Kosten bei der Verarbeitung von Metall anzuführen. Eine Kostenersparnis bringt derzeit nur die Verwendung von Kunststoffen, also Materialien mit geringerem Schmelzpunkt. Nachteilig ist auch die meist raue Oberfläche, die durch den schichtweisen Aufbau entsteht. Hier sind oft Nachbearbeitungsschritte nötig. Von der Stückzahl sind 3D-Druckverfahren bisher wirtschaftlich gesehen auf Kleinserien beschränkt.
Der Trend geht deshalb in Richtung Hybrid Manufacturing – hin zum hybriden Fertigungsprozess – bei dem die Stärken der beiden verschiedenen Ansätze miteinander kombiniert werden: die geometrische Komplexität additiver Verfahren und die hohe Präzision subtraktiver Methoden. So werden Bauteile zunächst im 3D-Druck erstellt und mittels entsprechender Werkzeuge spanend nachbearbeitet. Auf der anderen Seite integrieren viele Hersteller heutzutage einen Laserbearbeitungskopf in ihre CNC-Maschinen. Mit sogenannten Hybridmaschinen lassen sich beispielsweise Metallpulverbett- mit Fräsverfahren verbinden. In Zukunft wird es darum gehen, die Technologie nicht nur in Fabriken für additive Fertigung zu integrieren, sondern auch in gemischten, existierenden Fertigungsumgebungen. Dabei wird ein durchgängiger Daten- und Produktfluss ein wichtiges Thema sein.
Potenziale des Rapid Prototyping
Rapid Prototyping ist zu einer ernstzunehmenden Fertigungsmethode der Industrie 4.0 geworden, um Produkte effizienter und nachhaltiger herzustellen. Bisher werden die verschiedenen 3D-Druckverfahren vor allem dann eingesetzt, wenn geringe Stückzahlen, eine komplexe Geometrie oder ein hoher Grad der Individualisierung gefordert sind. Allerdings entwickelt sich die Technik rasant weiter – die Möglichkeiten der additiven Fertigung sind noch längst nicht ausgeschöpft.
Wir von der HS Development & Services GmbH sind dabei, das Potenzial der Technologie zu entdecken. Mit unserem FDM-Drucker testen wir die Materialvielfalt und nutzen die Flexibilität des Verfahrens, um innovative, funktionelle Objekte für unsere Kunden herzustellen.
In unserem nächsten Blogbeitrag geht es darum, das FDM-Druckverfahren in seiner Diversität genauer zu beleuchten und einen Einblick in unsere Arbeit zu geben.
Comentários